Слайд 2Введение в Лин - Понятия и основы - История возникновения - Принципы - Ценность, поток создания ценности, карта потока - Вытягивающее производство - Кайдзен - 8 видов потерь в потоке создания ценности
Содержание программы
Слайд 3Сокращение затрат за счет ликвидации потерь
Все, чем мы занимаемся, - это следим за временем между размещением заказа потребителем и получением денег за выполненную работу. Мы сокращаем этот промежуток времени, устраняя потери, которые не добавляют ценности. Тайити Оно , исполнительный вице-президент «Тойота Мотор Корпорейшн» (до 1978 г.)
Слайд 4Что такое Lean production (Лин)?
Lean – это системный подход к выявлению и устранению потерь путем непрерывного совершенствования, настройка производственных процессов в зависимости от потребностей клиента и стремление к безупречности во всем, начиная от организации рабочего места каждого сотрудника и заканчивая взаимоотношением с поставщиками и конечными потребителями. Lean в переводе с английского означает дословно «тощий, худой, постный, скудный». В России более популярен термин « Бережливое производство».
Слайд 5Термин «Lean production» был введен в США для обозначения базовых принципов организации TPS. Лин - это нацеленность системы на избавление на избавление организации от «ожирения», т.е. от любых непроизводительных затрат в процессе производства. Лин – это производство, в котором любые непроизводственные затраты сведены к минимуму или отсутствуют, т.е. все ресурсы предприятия используются только для создания потребительской ценности.
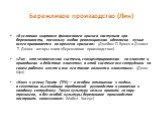
Слайд 6Бережливое производство (Лин)
«В условиях мирового финансового кризиса наступила эра бережливости, поскольку любая революционная идеология лучше всего приживается во времена кризисов» (Джеймс П. Вумек и Дэниел Т. Джонс - авторы книги «Бережливое производство») «Лин - это человеческая система, сконцентрированная на клиенте и приводимая в действие клиентом; в этой системе все сотрудники на своем рабочем месте и вне его также являются клиентами» (Джон Шук) «Ключ к успеху Toyota (TPS) — в особом отношении к людям, в сочетании высочайших требований руководства и уважения к каждому сотруднику. Такую культуру нельзя привить за пару тренингов, а без особой культуры бережливое производство построить невозможно» (Майкл Хосеус)
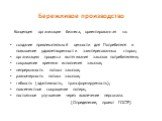
Слайд 7Бережливое производство
Концепция организации бизнеса, ориентированная на: создание привлекательной ценности для Потребителя и повышение удовлетворенности заинтересованных сторон; организацию процесса вытягивания заказов потребителями; сокращение времени исполнения заказов; непрерывность потока заказов; равномерность потока заказов; гибкость (адаптивность, трансформируемость); повсеместное сокращение потерь; постоянное улучшение через вовлечение персонала. (Определение, проект ГОСТР)
Слайд 8…система простых решений для выявления и устранения потерь с целью производства продукции и услуг с нужной скоростью и требуемым качеством для удовлетворения нужд потребителей. !!!Система Лин должна внедряться: всеми работниками во всех областях бизнеса.
Кратко: Система Лин это -
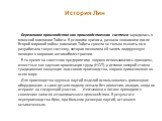
Слайд 9История Лин
Бережливое производство как производственная система зародилась в японской компании Тойота. В условиях кризиса, развала экономики после Второй мировой войны компания Тойота сумела не только выжить, но и разработала такую систему, которая позволила ей занять лидирующую позицию в мировом автомобилестроении. В то время на советских предприятиях широко использовались принципы, известные как научная организация труда (НОТ), у истоков которой стояла традиционная концепция массового производства, широко применяемая во всем мире. Для производства крупных партий изделий использовалось громоздкое оборудование, а сами детали подолгу лежали без движения, ожидая, когда их отправят на следующий участок. Нестыковки в потоке приводили к скоплению запасов незавершенного производства. В результате перепроизводства брак, при больших размерах партий, оставался незамеченным.
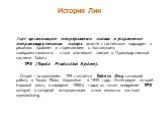
Слайд 10Идея организации непрерывного потока и устранения непроизводительных потерь вместе с системным подходом к решению проблем и стремлением к постоянному совершенствованию стали ключевым звеном в Производственной системе Тойота - TPS (Toyota Production System). Отцом - основателем TPS считается Тайити Оно, начавший работу в Toyota Motor Corporation в 1943 году. Интегрируя лучший мировой опыт, в середине 1950-х годов он начал внедрение TPS которая в западной интерпретации стала известна как Lean manufacturing.
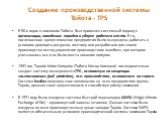
Слайд 11Создание производственной системы Тойота - TPS
В 50-х годах в компании Тойота был применен системный подход к организации, наведению порядка и уборке рабочего места. В то, послевоенное, время японские предприятия были вынуждены работать в условиях дефицита ресурсов, поэтому они разработали для своего производства метод управления производством «канбан», при котором учитывалось все и не было места никаким потерям. 1962 год Toyoda Motor Company (Тойота Мотор Компани) последовательно создает систему менеджмента TPS , основанную на концепции «вытягивания» (pull prodction), т.е. производства , основанного на спросе. Система Канбан получила свое воплощение на всех предприятиях группы Toyota, доказав свою эффективность и способствуя успеху компании. В 1971 году была внедрена система быстрой переналадки SMED (Single-Minute Exchange of Die) – одноминутной замены штампов. Данная система была внедрена во всех производственных цехах заводов Toyota. Система SMED является обязательным условием производственной системы компании Toyota.
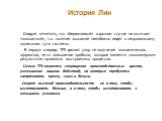
Слайд 12Следует отметить, что «бережливый» в данном случае не означает «экономный», т.к. понятие экономия неизбежно ведет к неправильному пониманию сути системы. В первую очередь TPS делает упор не получение экономических эффектов, не на повышение прибыли, которое является закономерным результатом правильно выстроенных процессов. Целью TPS является сокращение производственных циклов, уменьшение лишних действий, на которые требуется затрачивать время, силы и деньги. Секрет высокой производительности не в том, чтобы изготавливать больше, а в том, чтобы изготавливать с меньшими усилиями.
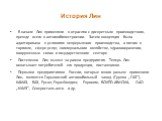
Слайд 13В начале Лин применяли в отраслях с дискретным производством, прежде всего в автомобилестроении. Затем концепция была адаптирована к условиям непрерывного производства, а потом в торговле, сфере услуг, коммунальном хозяйстве, здравоохранении, вооруженных силах и государственном секторе. Постепенно Лин вышел за рамки предприятия. Теперь Лин охватывает потребителей его продукции, поставщиков. Первыми предприятиями России, которые много раньше применили Лин, являются Горьковский автомобильный завод (Группа „ГАЗ"), КАМАЗ, ВАЗ, Русал, ЕвразХолдинг, Еврохим, ВСМПО-АВИСМА, ОАО „КУМЗ", Северосталь-авто и др.
Слайд 14Многие думают, что производственная система Тойоты – это набор инструментов: 5С, ТРМ, Канбан и пр. Но самое важное в этой системе – СПОСОБ МЫШЛЕНИЯ.
Инструменты Система
Мышление (философия, идеология)
Самое важное в Лин
Слайд 15преобразования в умах и чувствах людей
Внедрение Лин – это …
«Техническое» овладение инструментами 20%
Изменения в поведении и привычках 80%
Слайд 16Зачем внедрять Лин на предприятии?
Слайд 17
Слайд 18
Слайд 20Внедрение Лин (кратко)
1.Определение ценности 2.Определение потока создания ценности 3.Организация движения потока; 4.Создание системы вытягивания; 5.Совершенство. Кайдзен.
Слайд 211.Понятие ценности
Прежде всего система Лин направлена на удовлетворение запросов потребителей, поэтому определение ценности продукта является ключевым моментом. Под ценностью понимаются все основные характеристики продукции и услуги, которые потребитель хочет получить.
Слайд 23Требования потребителя (ценность)
Что такое ценность для потребителя?
Характеристики продукции прочность геометрические размеры цвет надежность и т.д.
Параметры услуги срок поставки ритм поставки объем каждой поставки возможность изменения требований к характеристиками продукции, объемам, срокам поставки и др.
Слайд 24• Добавление потребительской ценности всегда определяется с точки зрения заказчика – Кто наш заказчик? • Каждый процесс должен фокусироваться на добавлении потребительской ценности. Все, что не добавляет потребительской стоимости – потери. – Что на самом деле ценит заказчик? • Некоторые процессы, не добавляющие ценности - необходимы – Как их можно сократить?
Определение ценности
Слайд 252. Поток создания ценности
Поток создания ценности – все действия (как создающие ценность, так и не создающие ценности), которые позволяют продукту пройти все процессы: от разработки концепции продукта до запуска в производство и от принятия заказа до доставки. Данные действия включают в себя обработку информации, полученной от клиента, а также операции по преобразованию продукта по мере его продвижения к клиенту. Виды потоков: - материальный (сырье, материалы, полуфабрикаты, готовая продукция); - информационный (графики, планы, наряды, приказы в эл. виде или на бумажном носителе);
Слайд 263. Организуйте непрерывный поток, где это возможно
изолированно ресурсы запасы готовый продукт
непрерывный поток
Слайд 274. Вытягивающее производство
В Лин производство организовано так, чтобы поток добавления ценности был непрерывным. Сбои, помехи и остановки ведут к увеличению времени выполнения заказа, а излишние запасы мешают быстрому реагированию на ситуацию. Необходим не оптимальный уровень запасов, а такой, какой требует потребитель. Так реализуется «вытягивающая» система производства , т.е. мы производим только тогда, когда этого потребует последующая стадия потока. Принцип вытягивания означает, что мы производим только то, что «вытягивает» из нас потребитель.
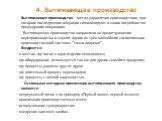
Слайд 28Вытягивающее производство – метод управления производством, при котором последующие операции сигнализируют о своих потребностях предыдущим операциям. Вытягивающее производство направлено на предотвращение перепроизводства и служит одним из трех важнейших составляющих производственной системы "точно вовремя". Внедряется: – в местах, где поток в одно изделие невозможен; – где оборудование используется так же для других семейств продуктов; – где процессы удалены друг от друга; – где длительный процесс переналадки; – где процессы с низкой надежностью. Основными методами организации вытягивающего производства являются: – непрерывный поток в по принципу «Первый вошел, первый вышел»; – организация производственных ячеек; – использование супермаркетов; – внедрение карточек канбан.
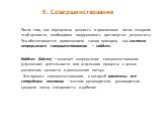
Слайд 295. Совершенствование
После того, как определена ценность и организован поток создания этой ценности, необходимо поддерживать достигнутые результаты. Это обеспечивается применением такого принципа, как система непрерывного совершенствования – кайдзен. Кайдзен (Kaizen) – означает непрерывное совершенствование (улучшение) деятельности или отдельного процесса с целью увеличения ценности и уменьшения потерь. Это процесс совершенствования, в который вовлечены все сотрудники компании – высшие руководители, руководители среднего звена, специалисты и рабочие.
Слайд 31Два подхода к улучшениям
Кайдзен улучшения постоянные, многочисленные, по отдельности – малые инвестиции не требуются
Инвестиционные инновации (модернизация, техперевооружение) реинжиниринг Эпизодические улучшения Основаны, как правило, на инвестициях
Слайд 32Соотношение ценность/ потери
Слайд 33
Слайд 34Мура (неравномерность, скачки в работе производственных процессов); Мури (чрезмерная нагрузка на рабочих оборудование ); Муда (потери) – излишнее производство, излишние запасы, излишнее движение, время ожидания, дефекты и переработка, излишняя транспортировка, излишняя обработка.
Проблемы в потоке создания ценности
Потери творческого потенциала!!!
Слайд 35Виды потерь
1. Перепроизводство – производство на склад в запас, без наличия заказа. 2. Избыток запасов на всех стадиях производства. 3. Лишняя транспортировка – перемещения сырья, полуфабрикатов, изделий на большие расстояния, между операциями, на склад и со склада. 4. Излишние перемещения – поиски, ходьба. 5. Ожидание – потери времени (ожидание, остановки оборудования, простой). 6. Излишняя обработка – неэффективная конструкция, технология, завышенные требования к качеству. 7. Дефекты – производство дефектных изделий. 8. Нереализованный творческий потенциал сотрудников.
Слайд 36
Слайд 37
Слайд 38
Слайд 39
Слайд 40
Слайд 41
Слайд 42
Слайд 43
Слайд 44
Слайд 45
Слайд 46
Слайд 47
Слайд 48
Слайд 49
Слайд 50Задачи на определение ценности, потерь. Задача № 1 Визит к врачу.
Слайд 51Задачи на определение ценности, потерь. Задача №2 Операции, выполняемые на сборочной линии шасси грузовых автомобилей