Слайд 1Легированные стали.
Легированными называют стали, в которые вводятся специальные легирующие элементы, способные улучшать механические, технологические, эксплуатационные свойства, а в некоторых случаях придавать стали особые физические или химические свойства. Легирующие элементы могут растворяться в феррите, аустените., цементите, образовывать специальные карбиды (карбиды легирующих элементов в отличии от карбида железа) или интерметаллидные соединения с железом и между собой, например, FeCr, FeV и т.д. Растворяясь в аустените или феррите, легирующие элементы упрочняют эти фазы, делают их более устойчивыми против распада при нагреве и охлаждении, изменяя температуры фазовых превращений и структуру сталей.
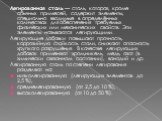
Слайд 2Легированная сталь — сталь, которая, кроме обычных примесей, содержит элементы, специально вводимые в определённых количествах для обеспечения требуемых физических или механических свойств. Эти элементы называются легирующими. Легирующие добавки повышают прочность, коррозийную стойкость стали, снижают опасность хрупкого разрушения. В качестве легирующих добавок применяют хром,никель, медь, азот (в химически связанном состоянии), ванадий и др. Легированную сталь по степени легирования разделяют на: низколегированную (легирующих элементов до 2,5 %), среднелегированную (от 2,5 до 10 %), высоколегированную (от 10 до 50 %).
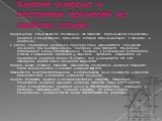
Слайд 3Влияние углерода и постоянных примесей на свойства сталей.
Углеродистые стали являются основными. Их свойства определяются количеством углерода и содержанием примесей, которые взаимодействуют с железом и углеродом. С ростом содержания углерода в структуре стали увеличивается количество цементита, при одновременном снижении доли феррита. Изменение соотношения между составляющими приводит к уменьшению пластичности, а также к повышению прочности и твердости. Прочность повышается до содержания углерода около 1%, а затем она уменьшается, так как образуется грубая сетка цементита вторичного. Углерод влияет на вязкие свойства. Увеличение содержания углерода повышает порог хладоломкости и снижает ударную вязкость. Повышаются электросопротивление и коэрцитивная сила, снижаются магнитная проницаемость и плотность магнитной индукции. Углерод оказывает влияние и на технологические свойства. Повышение содержания углерода ухудшает литейные свойства стали (используются стали с содержанием углерода до 0,4 %), обрабатываемость давлением и резанием, свариваемость. Следует учитывать, что стали с низким содержанием углерода также плохо обрабатываются резанием.
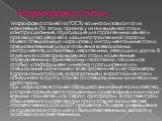
Слайд 4Маркировка стали.
Маркировка сталей по ГОСТу во многом зависит от их назначения. По этому признаку из них выделяют стали конструкционные, подходящие для строительных целей и производства деталей в машиностроительной отрасли. Имеют специальную маркировку инструментальные стали, предназначенные для изготовления всевозможных инструментов, штамповых, мерительных, режущих и других. В отдельную категорию выделяют стали, наделенные определенными физическими свойствами, такими как особый коэффициент линейного расширения или специальные магнитные и электротехнические параметры. Коррозионностойкие, жаропрочные и жаростойкие стали объединяют в группу сталей со специальными химическими свойствами. При маркировке сталей обращают внимание на их качество, которое определяется процентным содержанием в них таких вредных примесей, как сера с фосфором. В составе стали обыкновенного качества они присутствуют в количестве, соответственно, 0,06 и 0,07 процентов. По мере уменьшения их содержания стали могут быть качественными, высоко- и особовысококачественными.
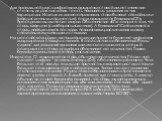
Слайд 5Для правильной расшифровки маркировки сталей имеет значение степень их раскисления, то есть показатель удаления из них кислорода. Исходя из данного признака, стали бывают спокойными (раскисленными полностью), они маркируются буквами «СП», проставляемыми после марки. Обозначение «КП» говорит о том, что сталь кипящая (слабораскисленная). А буквами «ПС» помечается сталь, находящаяся по своим показателям раскисления между спокойными и кипящими сталями. На российском рынке металлопродукции принята буквенно-цифровая маркировка сталей и сплавов. В этой системе обозначений буквы служат для указания названия химического элемента, который содержится в стали, а цифра обозначает его количество. Также буквами указывают степень раскисления. Индексом Ст маркируется сталь обыкновенного качества. После него следует цифра – условный номер (0-6), обозначающий марку. Чем больше этот номер, тем выше прочностные характеристики стали и больше содержащегося в ней углерода. Затем следует указание степени раскисления. Перед этими обозначениями проставляется индекс группы сталей: А, Б или В, причем для стали группы А индекс обычно не ставят. Буква «А» означает, что сталь гарантированных механических характеристик, «Б» - химического состава, «В» - имеет и то, и другое. Пример маркировки углеродистой стали обыкновенного качества, марки № 2, кипящей, поставляемой с гарантированными механическими свойствами: БСт2КП.
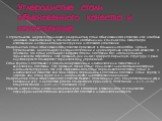
Слайд 6Углеродистые стали обыкновенного качества и качественные
В строительстве широко применяют углеродистые стали обыкновенного качества, как наиболе дешевые, технологичные и обладающие необходимым комплексом свойств при изготовлении многих металлоконструкций массового назначения. Углеродистые стали обыкновенного качества производят в больших масштабах. Кроме строительства, их используют в машиностроении и других отраслях народного хозяйства. В основном эти стали используют в горячекатаном состоянии без дополнительной термической обработки. Как правило, они имеют феррито-перлитную структуру. В ряде случаев прокат подвергают термическому упрочнению. Стали группы В поставляют с регламентированными механическими свойствами и химическим составом. Как правило, такие стали’ применяют для изготовления сварных металлоконструкций, так как свариваемость стали определяется составом стали, а механические свойства вне зоны сварки определены в состоянии поставки. Стали группу В дороже, чем стали групп А и Б, их применяют для ответственных изделий. Углеродистые стали обыкновенного качества бывают спокойными (сп), полуспокойными (пс) и кипящими (кп). В их составе разное содержание кремния, %: спокойные — 0,12—0,30, полуспокойные — 0,05—0,17; кипящие ^0,07. Каждая марка стали может иметь различную категорию в зависимости от количества нормируемых показателей химического состава и механических свойств.
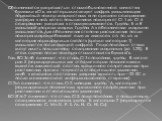
Слайд 7Обозначаются углеродистые стали обыкновенного качества буквами «Ст», за которыми следует цифра, указывающая порядковый номер марки стали, а не среднее содержание углерода в ней, хотя с повышением номера от Ст 1 до Ст 6 содержание углерода в стали увеличивается. Группы Б и В указывают впереди марки. Группа А в обозначении марки не указывается. Для обозначения степени раскисления после номера марки добавляют один из индексов сп, пс, кп, а категория нормируемых свойств (кроме категории 1) указывается последующей цифрой. Полуспокойиые стали могут иметь повышенное содержание марганца (до 1,2%). В этом случае после номера стали ставится буква «Г». Так, ВСтЗспб означает, что сталь СтЗ спокойная, группы В, категории 5 (нормируемыми для этой категории показателями являются: химический состав, временное сопротивление при растяжении, предел текучести, относительное удлинение, изгиб в холодном состоянии, ударная вязкость при —20 0C и после механического деформационного старения). Ст2кп означает, что сталь Ст2, кипящая, группы А, категории 1 (нормируемые показатели: временное сопротивление при растяжении и относительное удлинение). БСт5Гпс2 означает, что сталь Ст5, полуспокойная, с повышенным содержанием марганца, группы Б, категории 2 (нормируется содержание С, Mn, Si, Р, S, As, N, Cr, Ni, Cu).
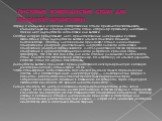
Слайд 8Листовые углеродистые стали для холодной штамповки.
Наряду с изделиями из прочных нагартованных сталей приходится изготавливать изделия из мягкой малоуглеродистой стали, например проволоку для обвязки, тонкий лист для глубокой штамповки или вытяжки. Особый интерес представляет лист, предназначенный для крыльев и кузовов автомобиля. Сталь для глубокой вытяжки должна отличаться большой пластичностью. Поэтому для этих целей применяют сталь с минимальным содержанием углерода. Действительно, для особо сложной штамповки содержание углерода ограничивается 0,08%.Существенно также ограничение содержания и других постоянных примесей (марганца, кремния, серы, фосфора), так как все они в той или иной степени уменьшают пластичность стали. Однако это ограничение (например, по марганцу) не должно ухудшать качество стали по другим показателям. Для глубокой вытяжки применяют преимущественно низкоуглеродистую кипящую (низцокремнистую) сталь марки 08 пк . Чтобы сталь хорошо штамповалась, она должна иметь не только определенный состав, но и соответствующую микроструктуру — мелкозернистый феррит с перлитом, располагающимся в стыках нескольких ферритных зерен. Коалесценция перлита ,приводит к появлению по границам зерен структурно свободного цементита, что вредно для штампуемости. Следуй отметить, что листы из кипящих малоуглеродистых сталей (в том числе марки 08 пк неоднородны, имеют расслоение, а также склонны к старению при комнатной температуре (за счет повышенного содержания кислорода). Поэтому наряду с кипящими сталями для этих целей применяют и спокойные или полуспокойные (успокоенные алюминием — марка 08 ю лишенные указанных недостатков, хотя и несколько более твердые.
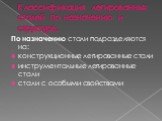
Слайд 9Классификация легированных сталей по назначению и структуре.
По назначению стали подразделяются на: конструкционные легированные стали инструментальные легированные стали стали с особыми свойствами
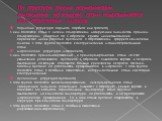
Слайд 10По структуре (после нормализации, охлаждение на воздухе) стали подразделяются на 5 структурных классов:
перлитный (структура перлита, сорбита или тростита) К ним относятся стали с низким содержанием легирующих элементов, средним содержанием углерода. На С-образной кривой линия охлаждения пересекает линии распада аустенита с образованием феррито-цементитых смесей. К этой группе относятся конструкционные машиностроительные стали. мартенситный (структура мартенсита) К ним относятся среднелегированные и среднеуглеродистые стали. За счет увеличения устойчивости аустенита, С-образная сдвигается вправо и скорость охлаждения на воздухе становится больше критической скорости закалки, поэтому аустенит на распадаясь превращается в мартенсит. К этой группе относятся стали с особыми свойствами, инструментальные стали, некоторые конструкционные. аустенитный (структура аустенита) К этой группе относятся высоколегированные, низкоуглеродистые стали. Легирующие элементы значительно сдвигают С-образную кривую вправо и понижают Мн в область отрицательных температур. Тогда аустенит охлаждается до комнатной температуры не распадаясь и не претерпевая мартенситное превращение. Т.о. в этих сталях аустенит сохраняется в структуре при комнатной температуре. К этой группе относятся стали с особыми свойствами (нержавеющие,жаростойкие).
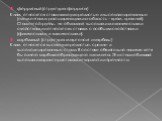
Слайд 11ферритный (структура феррита) К ним относятся стали низкоуглеродистые и высоколегированные (элементами, расширяющими α-область – хром, кремний). Стали этой группы, не обладают высокими механическими свойствами и относятся к сталям с особыми свойствами (физическими и химическими). карбидный (структура мартенсит и карбиды) К ним относятся высокоуглеродистые, средне- и высоколегированные стали. В составе обязательно наличие хотя бы одного карбидообразующего элемента. Эти стали обладают высокими характеристиками твердости и прочности.
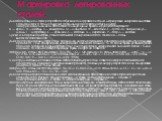
Слайд 12Маркировка легированных сталей.
Для обозначения марок разработана буквенно-цифровая система маркировки легированных сталей. Каждая марка стали содержит определенное сочетание букв и цифр. Легирующие элементы обозначают следующими буквами русского алфавита: X — хром, Н — никель, В — вольфрам, М — молибден, Ф — ванадий, Т — титан, Ю -алюминий, Д—медь, Г -- марганец, С — кремний, К — кобальт, Ц — цирконий, Р — бор, Б — ниобий. Буква А в середине марки стали показывает содержание азота, а в конце — сталь высококачественная. Для конструкционных марок стали первые две цифры показывают содержание углерода в сотых долях процента. Если содержание легирующего элемента больше 1 %, то после буквы указывается его среднее значение в целых процентах. Если содержание легирующего элемента около 1 % или меньше, то после соответствующей буквы цифра не ставится. Например, сталь 18ХГТ содержит, %: 0,18 С, 1 Сr, 1 Мn, около 0,1 Тi; сталь 38ХНЗМФА — 0,38 С, 1,2—1,5 Сr; 3 Ni, 0,3—0,4 Мо, 0,1—0,2 V; сталь 30ХГСА — 0,30 С, 0,8—1,1 Сr, 0,9—1,2 Мn, 0,8—1,251; сталь ОЗХ13АГ19 — 0,03 С, 13 Сr, 0,2—0,3 N. 19 Мn. В инструментальных сталях в начале обозначения марки стали ставится цифра, показывающая содержание углерода в десятых долях процента. Начальную цифру опускают, если содержание углерода около 1 % или более. Например, сталь 3Х2В8Ф содержит, % 0,3 С, 2 Cr, 8 XV, 0,2—0,5 V; сталь 5ХНМ —0,5 С, 1 Cr, 1 N1, до 0,3 Мо; сталь ХВГ— 1 С, 1 Cr, 1 ТС, 1 Мn. Для некоторых групп сталей принимают дополнительные обозначения, Марки автоматных сталей начинаются с буквы А, подшипниковых — с буквы Ш, быстрорежущих — с буквы Р, электротехнических — с буквы Э, магнитно-твердых — с буквы Е. Нестандартные легированные стали, выпускаемые заводом «Электросталь», обозначают сочетанием букв ЭИ (электросталь исследовательская) или ЭП (электросталь пробная). Легированные стали, выпускаемые Златоустовским металлургическим заводом — буквами ЗИ. Во всех случаях после сочетания букв идет порядковый номер стали, например, ЭИ417, ЭП67, ДИ8 и т. д. После освоения марки металлургическими и машиностроительными заводами условные обозначения заменяет общепринятая маркировка, отражающая химический состав стали.
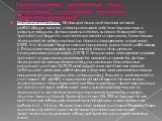
Слайд 13Конструкционные легированные стали: цементуемые, улучшаемые, пружинные, шарикоподшипниковые.
Цементуемые стали. Используются для изготовления деталей, работающих на износ и подвергающихся действию переменных и ударных нагрузок. Детали должны сочетать высокую поверхностную прочность и твердость и достаточную вязкость сердцевины. Цементации подвергаются низкоуглеродистые стали с содержанием углерода до 0,25%, что позволяет получить вязкую сердцевину. Для деталей, работающих с большими нагрузками, применяются стали с повышенным содержанием углерода (до 0,35 %). С повышением содержания углерода прочность сердцевины увеличивается, а вязкость снижается. Детали подвергаются цианированию и нитроцементации. Цементуемые углеродистые стали 15,20,25 используются для изготовления деталей небольшого размера, работающих в условиях изнашивания при малых нагрузках (втулки, валики, оси, шпильки и др.). Твердость на поверхности составляет 60…64 HRC, сердцевина остается мягкой. Цементуемые легированные стали применяют для более крупных и тяжелонагруженных деталей, в которых необходимо иметь, кроме высокой твердости поверхности, достаточно прочную сердцевину (кулачковые муфты, поршни, пальцы, втулки). Хромистые стали 15Х, 20Х используются для изготовления небольших изделий простой формы, цементуемых на глубину h =1…1,5 мм. Вследствие этого хромистые стали обладают более высокими прочностными свойствами при несколько меньшей пластичности в сердцевине и большей прочностью в цементованном слое.
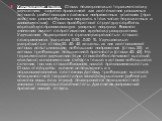
Слайд 14Улучшаемые стали. Стали, подвергаемые термическому улучшению, широко применяют для изготовления различных деталей, работающих в сложных напряженных условиях ( при действии разнообразных нагрузок, в том числе переменных и динамических). Стали приобретают структуру сорбита, хорошо воспринимающую ударные нагрузки. Важное значение имеет сопротивление хрупкому разрушению. Улучшению подвергаются среднеуглеродистые стали с содержанием углерода 0,30…0,50 %. Улучшаемые углеродистые стали 35, 40, 45 дешевы, из них изготавливают детали, испытывающие небольшие напряжения (сталь 35), и детали, требующие повышенной прочности (стали 40, 45). Но термическое улучшение этих сталей обеспечивает высокий комплекс механических свойств только в деталях небольшого сечения, так как стали обладают низкой прокаливаемостью. Стали этой группы можно использовать и в нормализованном состоянии. Детали, требующие высокой поверхностной твердости при вязкой сердцевине (зубчатые колеса, валы, оси, втулки), подвергаются поверхностной закалке токами высокой частоты. Для снятия напряжений проводят низкий отпуск.
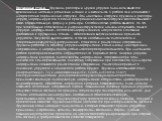
Слайд 15Пружинные стали. Пружины, рессоры и другие упругие элементы являются важнейшими деталями различных машин и механизмов. В работе они испытывают многократные переменные нагрузки. Под действием нагрузки пружины и рессоры упруго деформируются, а после прекращения действия нагрузки восстанавливают свою первоначальную форму и размеры. Особенностью работы является то, что при значительных статических и ударных нагрузках они должны испытывать только упругую деформацию, остаточная деформация не допускается. Основные требования к пружинным сталям – обеспечение высоких значений пределов упругости, текучести, выносливости, а также необходимой пластичности и сопротивления хрупкому разрушению, стойкости к релаксации напряжений. Пружины работают в области упругих деформаций, когда между действующим напряжением и деформацией наблюдается пропорциональность. При длительной работе пропорциональность нарушается из-за перехода части энергии упругой деформации в энергию пластической деформации. Напряжения при этом снижаются. Самопроизвольное снижение напряжений при постоянной суммарной деформации называется релаксацией напряжений. Релаксация приводит к снижению упругости и надежности работы пружин. Пружины изготавливаются из углеродистых (65, 70) и легированных (60С2, 50ХГС, 60С2ХФА, 55ХГР) конструкционных сталей. Для упрочнения пружинных углеродистых сталей применяют холодную пластическую деформацию посредством дробеструйной и гидроабразивной обработок, в процессе которых в поверхностном слое деталей наводятся остаточные напряжения сжатия. Повышенные значения предела упругости получают после закалки со средним отпуском при температуре 400…480 oС. Для сталей, используемых для пружин, необходимо обеспечить сквозную прокаливаемость, чтобы получить структуру троостита по всему сечению. Упругие и прочностные свойства пружинных сталей достигаются при изотермической закалке. Пружинные стали легируют элементами, которые повышают предел упругости – кремнием, марганцем, хромом, вольфрамом, ванадием, бором. В целях повышения усталостной прочности не допускается обезуглероживание при нагреве под закалку и требуется высокое качество поверхности.
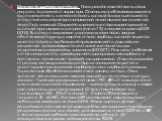
Слайд 16Шарикоподшипниковые стали. Подвергаются воздействию высоких нагрузок переменного характера. Основными требованиями являются высокая прочность и износостойкость, высокий предел выносливости, отсутствие концентраторов напряжений, неметаллических включений, полостей, ликваций. Шарикоподшипниковые стали характеризуются высоким содержанием углерода (около 1 %) и наличием хрома (ШХ9, ШХ15). Высокое содержание углерода и хрома после закалки обеспечивает структуру мартенсит плюс карбиды, высокой твердости, износостойкости, необходимой прокаливаемости. Дальнейшее увеличение прокаливаемости достигается дополнительным легированием марганцем, кремнием (ШХ15СГ). Повышены требования в отношении чистоты и равномерности распределения карбидов, в противном случае может произойти выкрашивание. Стали подвергаются строгому металлургическому контролю на наличие пористости, неметаллических включений, карбидной сетки, карбидной ликвации. Термическая обработка включает отжиг, закалку и отпуск. Отжиг проводят после ковки для снижения твердости и подготовки структуры к закалке. Температура закалки составляет 790…880 oС в зависимости от массивности деталей. Охлаждение – в масле (кольца, ролики), в водном растворе соды или соли (шарики). Отпуск стали проводят при температуре 150…170oС в течение 1…2 часов. Обеспечивается твердость 62…66 НRC. Из стали ШХ9 изготавливают шарики и ролики небольших размеров, из стали ШХ15 – более крупные. Детали подшипников качения, испытывающие большие динамические нагрузки (подшипники прокатных станов), изготавливают из сталей 20Х2Н4А и 18ХГТ с последующей глубокой цементацией на глубину 5…10 ммагрессивных средах, используется сталь 95Х18.
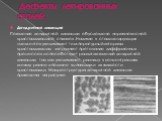
Слайд 17Дефекты легированных сталей.
Дендритная ликвация Появление дендритной ликвации обусловлено неравновесной кристаллизацией сплавов .Наличие в стали легирующих элементов увеличивает температурный интервал кристаллизации, затрудняет протекание диффузионных процессов и способствует развитию явлений дендритной ликвации, так как увеличивает разницу в концентрациях между ранее и позднее выпавшими из жидкости кристаллами. Макроструктура дендритной ликвации приведена на рисунке
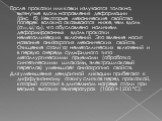
Слайд 18После прокатки или ковки излучаются толокна, вытянутые вдоль направления деформации (рис. б). Некоторые механические свойства поперек волокна оказываются ниже, чем вдоль (σ02, ψ, aH), чго обусловлено наличием деформированных вдоль прокатки неметаллических включений. Это явление носит название анизотропия механических свойств. Очищение стали от неметаллических включений и в первую очередь сульфидного типа металлургическими приемами (обработка синтетическими шлаками, электрошлаковый переплав) уменьшает анизотропию свойств. Для уменьшения дендритной ликвации прибегают к диффузионному отжигу слитков перед прокаткой, который состоит в длительном нагреве стали при весьма высоких температурах (1000 ÷ 1200 °С).
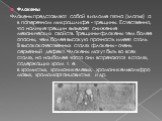
Слайд 19Флокены Флокены представляют собой в изломе пятна (хлопья) а в поперечном микрошлифе - трещины. Естественно, что наличие трещин вызывает снижение механических свойств. Трещины-флокены тем более опасны, чем более высокую прочность имеет сталь. В высококачественных сталях флокены - очень серьезный дефект. Флокены могут быть во всех сталях, но наиболее часто они встречаются в сталях, содержащих хром т. е. в хромистых, хромоникелевых, хромоникельвольфрамовых, хромомарганцовистых и др.
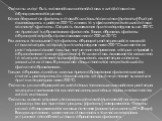
Слайд 20Флокены могут быть в кованой или катаной стали, в литой стали они обнаруживаются редко. Когда появляются флокены в стали:Если сталь после ковки (прокатки) быстро охлаждалась в районе 200 °С и ниже, то у флокеночувствительной стали возникнут флокены. Скорость охлаждения при температурах выше 200 °С не приводит к образованию флокенов. Таким образом, флокены образуются при быстром охлаждении от 200 до 20 °С. Ряд данных показывает, что флокены образуют растворившийся в жидкой стали водород, который при температурах ниже 200 °С выделяется из раствора и создает сильные внутренние напряжения, которые и приводят к образованию трещин (флокенов). Если же сталь охлаждается медленно, то водород успевает продиффундировать из раствора и совсем удалиться из стали. В результате сталь становится нечувствительной к флокенообразованию . Таким образом, одной из главных причин образования флокенов можно считать растворенный в стали водород, который не успевает выделиться при температурах ниже 200 °С. Флокены редко образуются в литой стали, так как выделившийся из раствора водород скапливается в многочисленных литейных порах и неплотностях литого металла. Флокены можно устранить последующей ковкой (прокаткой) на меньший размер, так как при этом трещины (флокены) завариваются. Флокены редко обнаруживаются в малых сечениях (диаметром менее 25 ÷ 30 мм). Вакуумирование, удаление из стали газов, в том числе водорода устраняет способность стали к образованию флокенов.